Static electricity is a silent adversary when it comes to handling plastic materials, yet it's a hurdle that can be overcome with the right expertise and approach. Residents and businesses alike often grapple with static cling or discharges which can interfere with work efficiency and product performance. The good news is that several effective strategies exist to mitigate or eliminate the issues of static electricity in plastics.
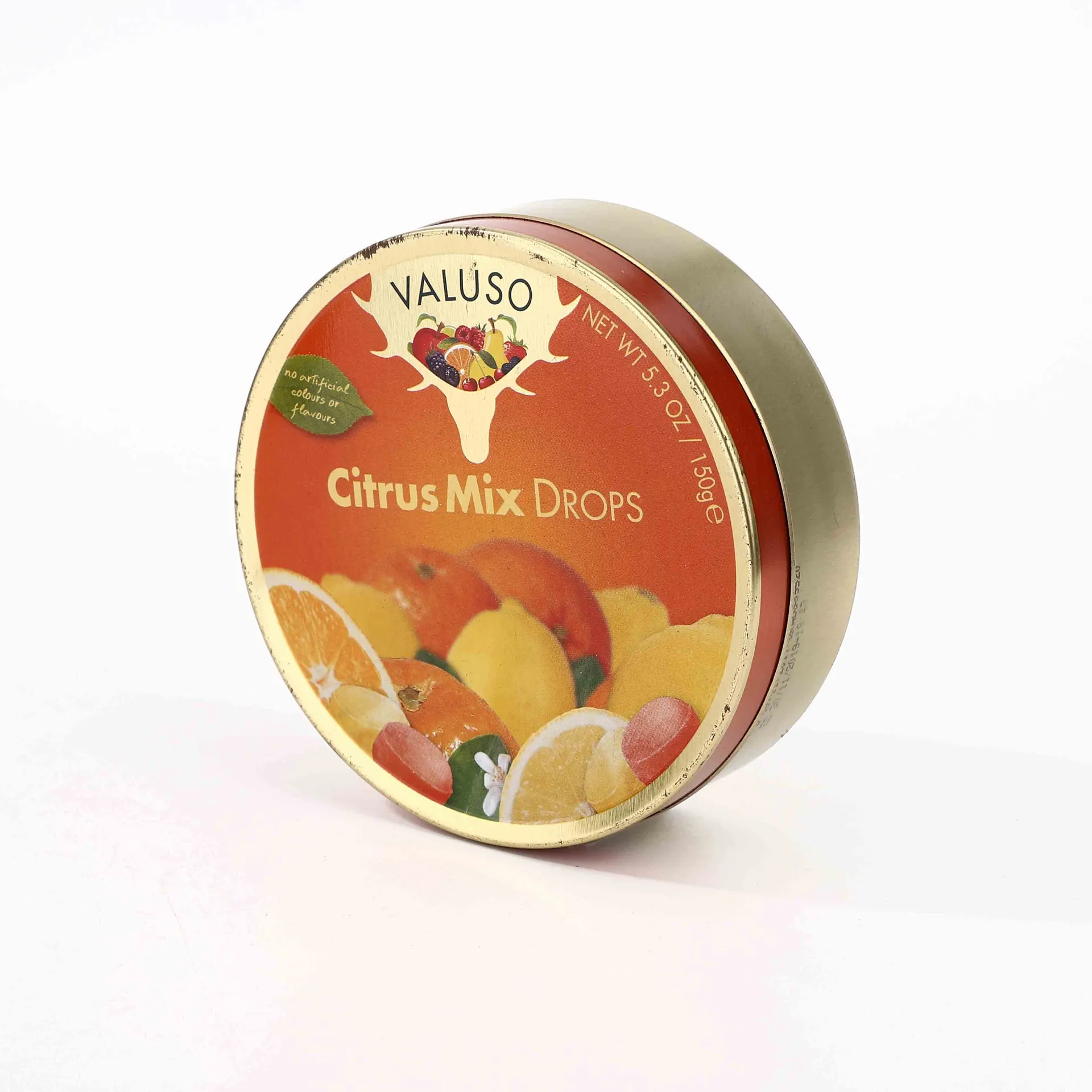
Plastic materials, by their very nature, are insulators. This means they don’t easily allow the flow of electricity. When two materials come into contact and then separate, electrons can transfer between them, causing an imbalance. The plastic ends up with a static charge as a result of this electron exchange. This static can attract dust or, worse, create shocks that damage electronic components.
Dealing with static in plastics requires understanding the environment and the materials involved.
One practical approach to mitigate static electricity is the use of antistatic agents. These are chemical additives that can be incorporated into plastics to reduce their tendency to generate static charge. These agents work by absorbing moisture from the atmosphere, which increases the conductivity of the plastic's surface and allows the static charge to dissipate.
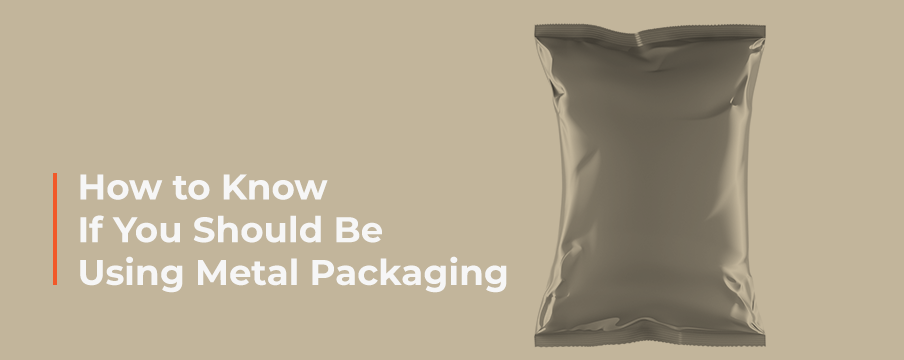
However, not all antistatic agents are created equal. Choosing the appropriate agent depends on factors such as the type of plastic, the environment in which it is used, and any regulatory requirements for the end product. For example, in environments where food contact is possible, only food-grade antistatic agents should be considered to ensure compliance with health standards.
In addition to antistatic agents, incorporating conductive fillers such as carbon black into the plastic during manufacturing can significantly reduce static buildup. These fillers create a conductive network within the plastic, which allows static electricity to dissipate more rapidly. Conductive fillers are most effective in closed system environments, like electronic housings, where static discharge can cause critical failures.
For a more environmentally friendly approach, companies may opt for mechanical or physical methods to minimize static. Humidifying environments where plastic materials are stored or processed is a simple yet effective method. The increased moisture content in the air helps charge dissipation. However, this method works best indoors where humidity levels can be controlled.
best remove static from plastic
Another effective tool is ionization. Ionizers can be installed in workspaces to emit ions that neutralize the charges on a plastic’s surface, thus eliminating static buildup. They are especially useful in precision manufacturing environments, where static charges can skew the results or damage sensitive electronic components.
Professionals in plastic manufacturing industries also recommend regular monitoring and maintenance of equipment. Machines that handle plastics should be earthed (grounded) properly to ensure that static charges have a safe path to dissipate. Routine checks for grounding effectiveness and timely maintenance of grounding equipment can make a significant difference in static management.
It's pertinent to remember that addressing static electricity challenges in plastics is not a one-size-fits-all scenario. A comprehensive approach considering specific environmental conditions, plastic material properties, and product end-use requirements will lead to the most effective static management strategy. Consulting with material and electrical engineers may provide additional insights and tailored solutions specific to your needs.
Building expertise in this field involves not only understanding the science behind static electricity but also being conversant with the latest industry tools and technologies. Staying informed through continuous education and engagement in professional groups or forums can offer advantages in problem-solving and innovation.
In conclusion, managing static in plastics is achievable by combining expert knowledge with practical solutions. Whether through chemical, physical, or mechanical means, ensuring that the approach is suited to the specific plastic and its application will yield the best results. Eliminating static electricity will not only improve product performance and employee safety but also enhance the reliability and trustworthiness of the products made.