In the world of packaging, the oft-overlooked tin can plays a pivotal role in preserving, protecting, and presenting products, especially in the food and beverage industry. A standard tin can, while seemingly simple, is a marvel of engineering and design, tailored to meet specific demands and functions.
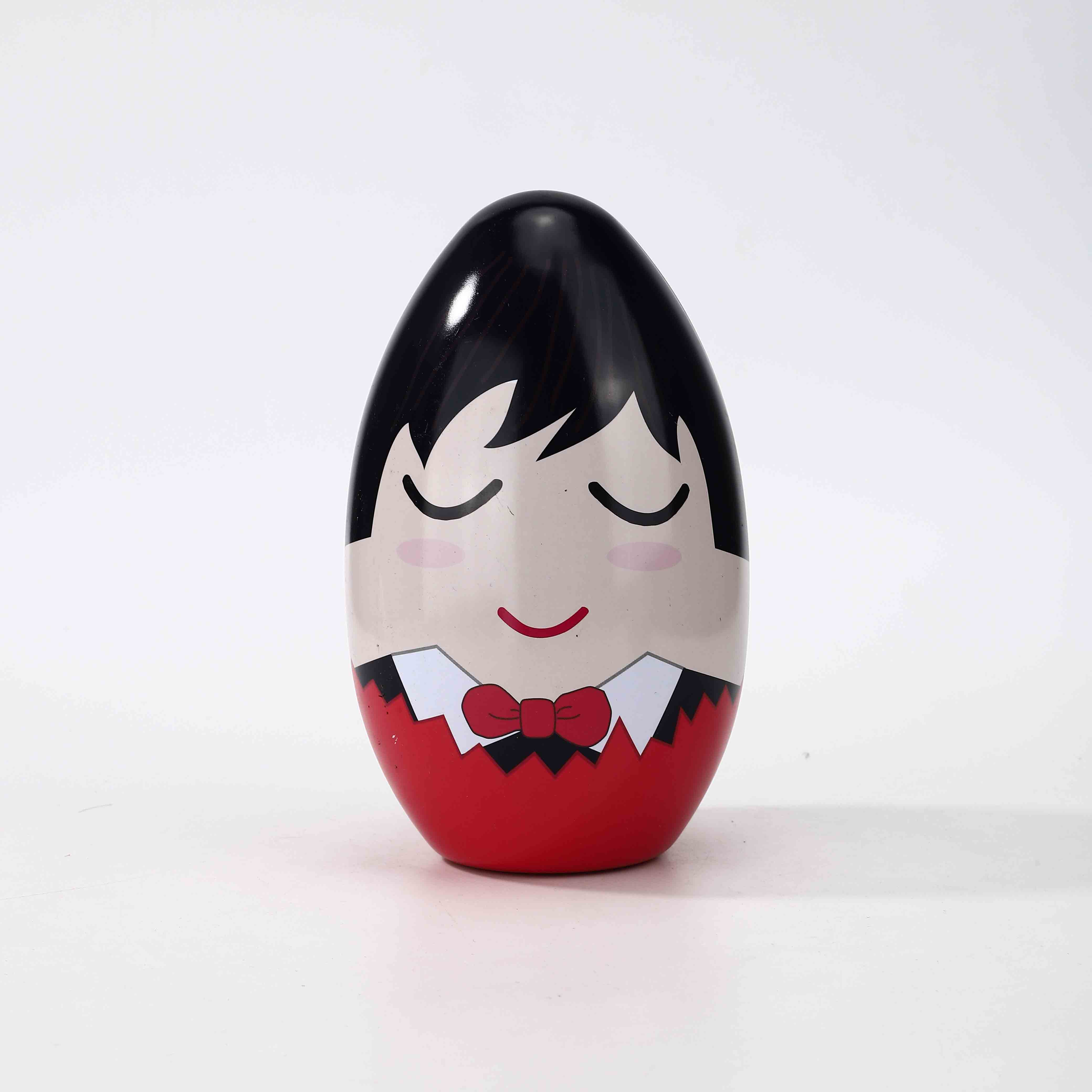
At its core, the standard tin can must balance durability with practicality. Typically, the dimensions of a standard tin can are based on its intended purpose. For example, a common size might be a can with a capacity of 355 ml for beverages, recognized for its efficiency in packing and shipping. Its dimensions usually translate to a height of approximately 4.83 inches and a diameter of 2.13 inches. These measurements have been optimized over decades to ensure that the can uses minimal material while maximizing internal space and sturdiness.
A deeper dive into the material science reveals that the can's walls, often just 0.33 mm thick, are crafted for both strength and flexibility. This thickness can withstand various pressures and handling during transport. Manufacturers employ a process known as draw and iron, which stretches and thins the metal into its desired shape. This method not only ensures uniformity but also heightens the can's resilience to impacts, an essential aspect for maintaining the integrity of its contents.
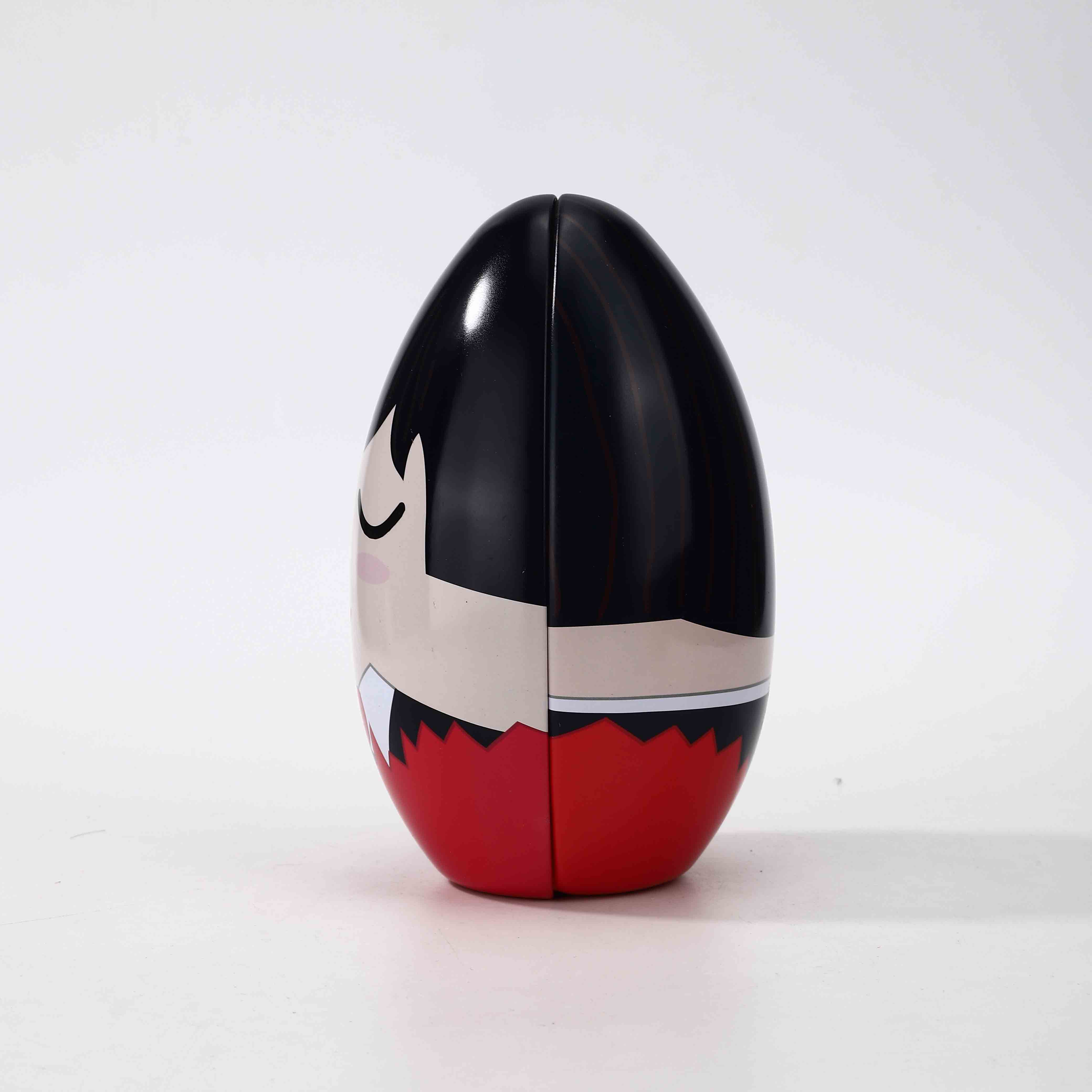
Moreover,
the standardization of tin can dimensions is pivotal for global trade and logistics. Uniform dimensions mean that products can seamlessly traverse international borders and storage facilities without the hiccup of custom solutions. This is a major advantage for companies looking to distribute their products widely and efficiently. A standardized can size contributes to reducing the costs associated with transport and storage by maximizing the number of cans that can fit within a crate or container.
standard tin can dimensions
But the standard tin can is not just about dimensions and logistics—it encompasses sustainability. As industries shift towards more eco-conscious practices, the recyclable nature of tin cans stands out. These cans are predominantly made from steel, coated with a thin layer of tin to prevent corrosion. This not only extends the life of the container but also ensures it remains recyclable down to nearly every part. The steel industry has developed precise recycling processes, meaning tin cans are one of the most recycled packaging forms worldwide, aligning with sustainability goals.
Innovations in can design also cater to consumer convenience. For instance, the advent of pull-tab lids revolutionized the user experience, eliminating the need for can openers and making the product more accessible. Today, a can's design must consider not just these practical aspects, but also how it showcases and preserves more nuanced qualities such as flavor and freshness—an imperative for premium food brands vying for consumer trust and loyalty.
In conclusion, the standard tin can dimensions are more than a mere specification; they embody a legacy of innovation, efficiency, and sustainability. For companies within the packaging sphere, understanding and utilizing these cans to their full potential can play a crucial role in minimizing costs, ensuring consumer satisfaction, and upholding a commitment to the environment. This deceptively simple container is a testament to the foresight and ingenuity of engineers and manufacturers aiming to meet the complex demands of the modern world.